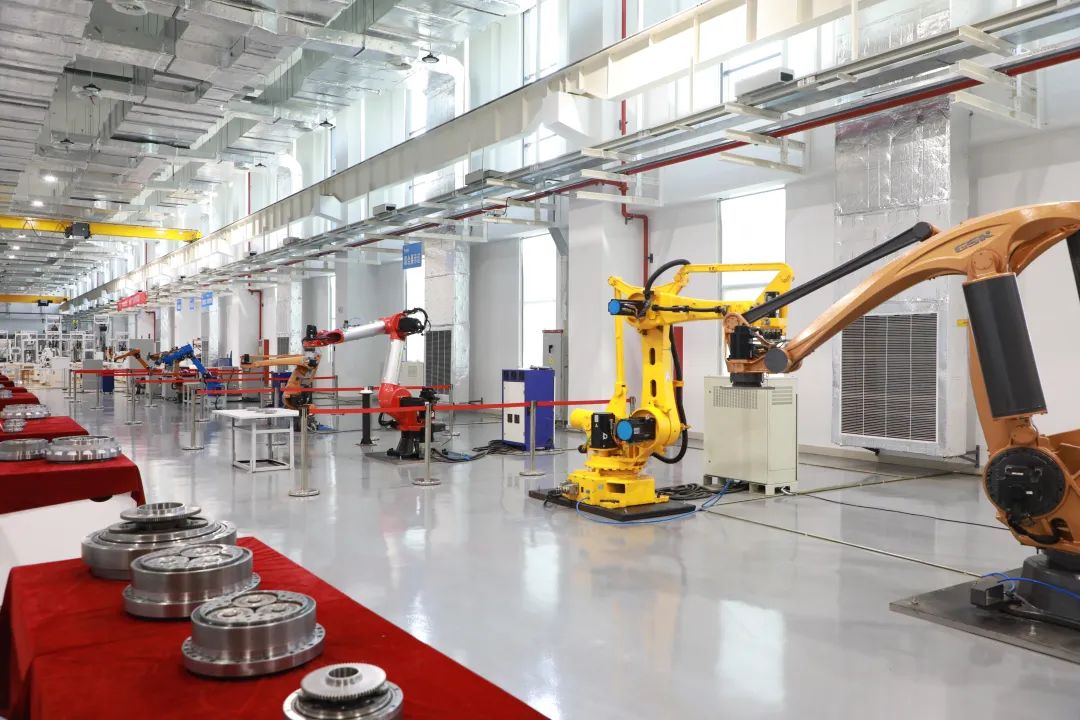
破瓶頸 打造工業機器人關節減速器國產化裝備
一臺工業機器人,伺服電機、控制器、減速器是其最核心的三個關鍵零部件,而機器人關節減速器因其傳動比范圍大、精度較穩定、疲勞強度較高,且具有更高的剛性和扭矩承載力,廣泛用于機器人機座、大臂、肩部等重負載的位置,但也因此,在設計上需要使用更為復雜的過定位結構,制造工藝和成本控制難度較大,且對于減速器類產品的制造設備受到極大限制。
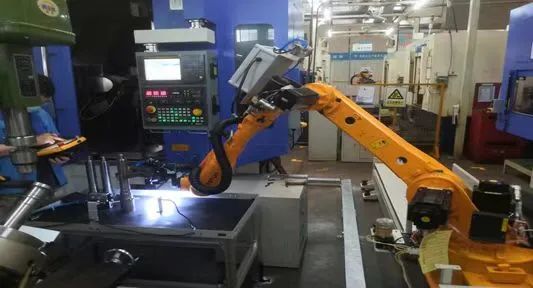
為打破行業壟斷,制造具有中國品牌的機器人核心零部件,秦川集團充分發揮公司復雜型面數字制造工藝裝備優勢,針對機器人關節減速器的兩級行星齒輪傳動系統,即漸開線外嚙合行星齒輪傳動和擺線針輪行星傳動,確定了針對擺線輪、針齒殼、偏心軸、行星架和行星齒輪5大零部件的關鍵工藝,研發出了MK2336、VG80、QYF007、QYF007T等專用加工裝備,對于機器人關節減速器在精加工階段的關鍵設備高精度磨齒機,秦川集團更是有在高端數控機床領域與國外品牌角力的能力和底氣。作為機床工具行業的龍頭企業,公司磨齒機產品被工信部評為“制造業單項冠軍”,其齒輪加工機床市場占有率超過60%。公司研發的YK7332AT數控高效成形磨齒機可以對擺線齒輪、針齒殼、漸開線圓柱齒輪和花鍵等零件進行高精度加工,解決減速器關鍵零件加工的“卡脖子”問題。秦川集團得天獨厚的裝備制造優勢既可以實現減速器供應鏈的安全保障,同時產品的工藝迭代還可隨著精密磨齒機等設備的升級而實現更高品質。
做標準 構筑秦川特有的技術壁壘
由于工業機器人減速器高精度、高剛度的特點,以及批量化生產的工藝、設備沒有現成經驗可循,秦川集團從一開始就堅持正向研發,在守正中創新,走直線追趕之路。
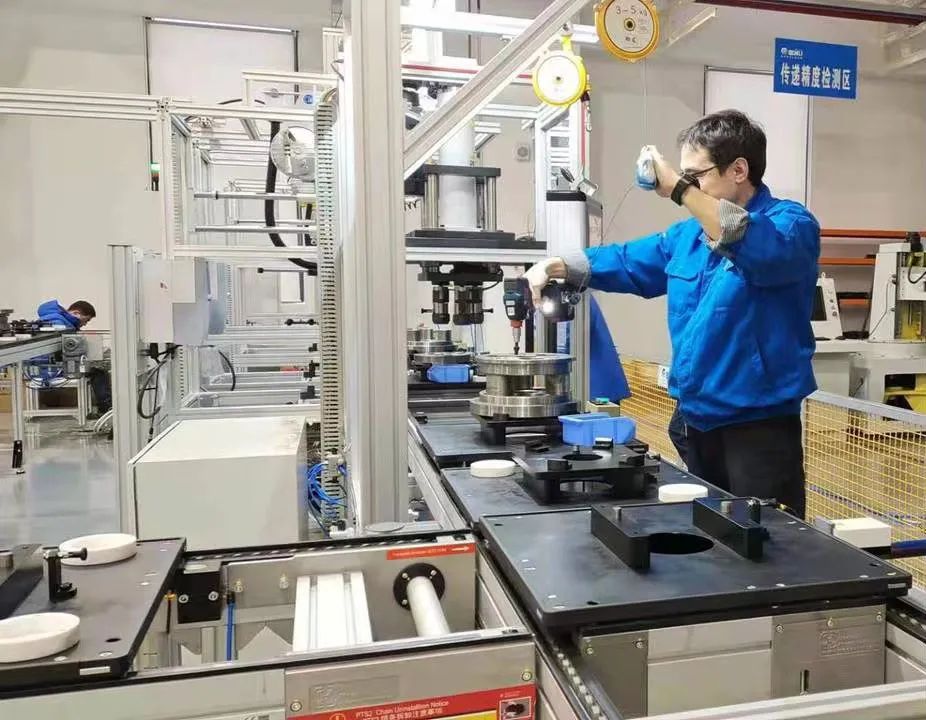
為了滿足用戶定制化需求,為用戶提供全方位解決方案,秦川集團提出自主研發減速器數字化正向設計平臺,以快速滿足多品種、換型快的市場需求,實現減速器產品的數字化生產和服務。依托五十多年在齒輪傳動、研發、設計、鑄造、熱處理、制造、檢測和試驗的經驗積累,秦川集團采用具有國際先進水平的齒輪傳動系統設計軟件及有限元分析系統進行正向研發,依據載荷譜進行減速器產品數字化建模、裝配和虛擬樣機仿真,對樣機的設計、加工、裝配、試驗等數據進行分析優化,形成數字化的減速器產品,之后,進行機器人運行試驗、振動分析、運動仿真、姿態調整等工作,并獲得減速器的相關數據,最后,通過測試試驗結果對數字化正向設計虛擬樣機進行再優化和再調整,從而達到減少試驗次數,縮短試驗的流程,提高新產品研發水平的目的。通過正向設計,可與實際的測試驗證重合度達到96%以上。
在直道追趕中,秦川集團憑借國內關節減速器聯盟標準主要單位身份起草《機器人用精密擺線行星齒輪減速器》標準,進一步脫穎而出,掌握了該領域話語權。目前,公司牽頭和參與起草國家和行業標準4項,獲授權專利8項;作為國內機器人關節減速器第一方陣企業,2022年,該公司參與申報的“工業機器人精密減速器測試方法與性能提升技術研究”項目榮獲中國機械工業科學技術獎一等獎(科技進步獎)。
舉全力 做強核心零部件產業的“主力軍”
數據顯示,2021年我國工業機器人減速器總需求量為93.11萬臺,同比增長78.06%。其中增量需求82.41萬臺,同比增長95.05%;存量替換量為10.70萬臺,同比增長6.57%。面對巨大的國產替代空間,秦川集團將工業機器人關節減速器項目作為集團“5221”戰略布局中高端制造領域的重點支撐,并舉集團全力將其打造為核心零部件產業的“主力軍”。
2018年,秦川集團開工建設工業機器人關節減速器廠房2.8萬㎡,生產作業面積2.2萬㎡,累計投入各類加工、檢測、測試設備150臺(套),為機器人關節減速器產業提升產能打下堅實基礎。
2020年,公司發布公告以 4.29億元收購沃克齒輪100%股權,沃克齒輪作為集團最大的產品中試基地,一方面可以對公司的機床產品進行及時的反饋升級迭代,助力公司研發性能更優的減速器產品;另一方面,沃克齒輪在齒輪制造方面優秀的技術積累及規模化的生產經驗,也能助力公司機器人關節減速器業務規模化生產及優化成本質量。比如,對于減速器關鍵零件材料,秦川集團利用沃克齒輪在熱處理方面的技術優勢,成功解決減速器關鍵零件新材料在熱處理方面的瓶頸,其耐磨性測試表明,使用新材料后,傳動精度和反向間隙數據強基項目研發新材料明顯優于老材料。
此外,集團還依托秦川數控和秦川思源量儀的一體化測控技術開發與設備研制領域的能力,根據機器人減速器的產品要求,自主設計制造了機器人減速器產品試驗臺,包括零部件測量平臺和整機測試平臺,通過實驗室測試及部分客戶的掛機實驗,回轉精度、剛度要求等性能指標完全滿足設計要求,并得到用戶認可。
截止2021年,秦川集團工業機器人關節減速器約占到國產同類產品品牌市場份額的20%-25%,產品在國內外機器人本體制造商及集成商中得到廣泛應用,部分型號產品已實現小批量出口。